New organs.
Creating a new pipe organ is a harmonious blend of artistry and precision engineering, requiring superb attention to detail and a broad understanding of both musical and spatial dynamics. From the initial design phase to the final installation, every step in the process is guided by Greenleaf’s commitment to excellence, and our appreciation and reverence for the centuries-old tradition of organ building.
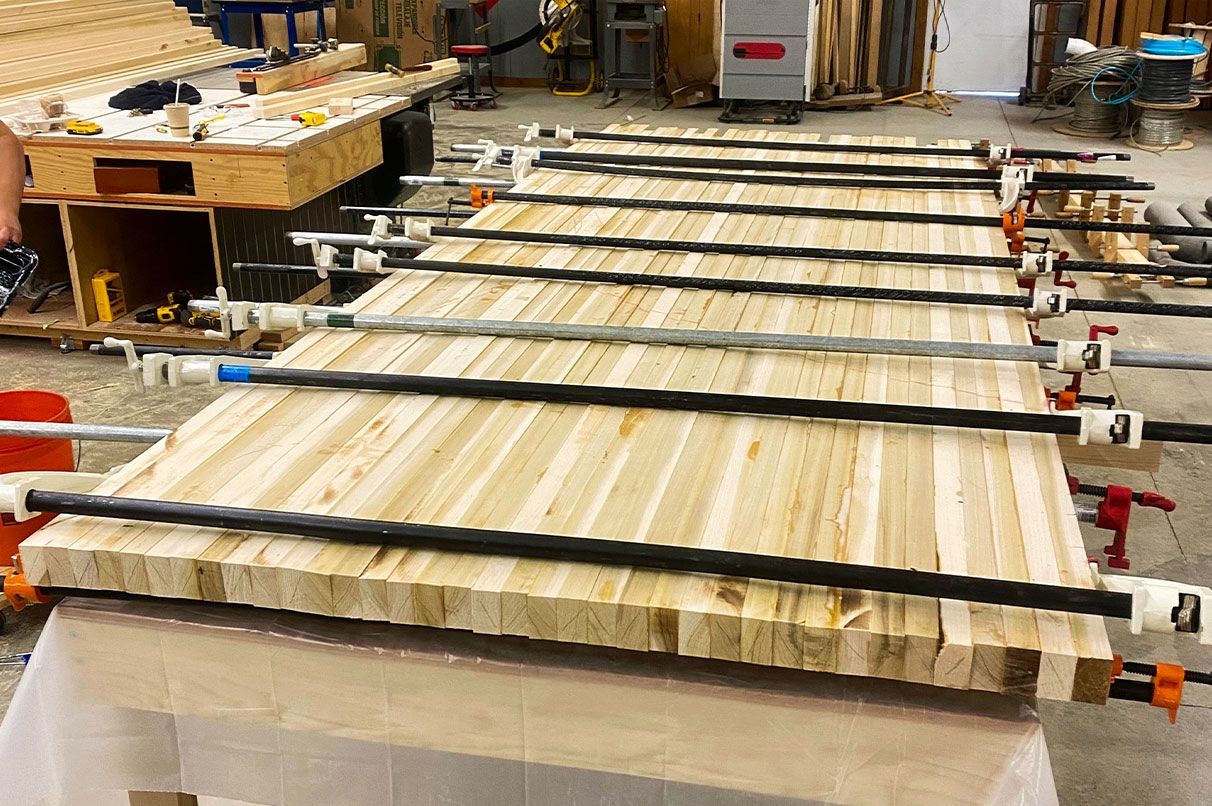
The first step towards new slider windchest toeboard construction: this slab will ‘rest’ for four months before use.
Designing a new organ.
The design for a new organ is a synthesis of many elements that must be considered. At the core of the process lies a deep understanding of the client's musical and tonal ideals, and the intended use of the instrument. Many factors play a crucial role in shaping the organ's design such as the size and acoustical volume of the space, the nature of the liturgical, ceremonial, and musical activities that occur, as well as the available area for installation.
Additionally, the visual integration of the organ with the surrounding environment, whether blending in seamlessly or standing out intentionally, is carefully studied.